The race for dependability: Missed opportunities in the Philippines’ oil and gas industry
AS GLOBAL ATTENTION shifts towards renewable energy and achieving net-zero emissions, the oil and gas industry’s potential to improve operational efficiency in meeting demand often gets sidelined. In the Philippines, where the goal is to achieve net-zero emissions by 2050, oil and gas will remain essential to the energy mix for the foreseeable future. Pressure […]
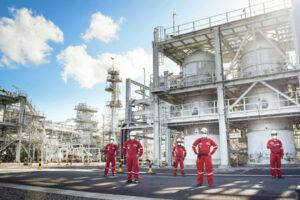
AS GLOBAL ATTENTION shifts towards renewable energy and achieving net-zero emissions, the oil and gas industry’s potential to improve operational efficiency in meeting demand often gets sidelined. In the Philippines, where the goal is to achieve net-zero emissions by 2050, oil and gas will remain essential to the energy mix for the foreseeable future.
Pressure is already high; for electricity, the Philippines relies heavily on coal and natural gas acquired from the Malampaya gas field, which is expected to run dry in 2027. Yet, in the short-term, renewable energy is unlikely to bridge the intermittency gap. Balancing energy supply with emission reduction is a significant challenge, but with the added pressure of exponentially increasing electricity demand, enhancing the efficiency and dependability of existing infrastructure is equally critical.
NEW AVENUE FOR REGIONAL LEADERSHIP
The Philippines continues to play a strategic role in the regional oil and gas industry, particularly in downstream activities such as refinery and distribution. The country’s focus on modernizing its refineries includes significant upgrades to the Bataan refinery, the country’s largest.
However, the nation struggles with aging infrastructure and maintenance issues, particularly in the downstream sector. Challenges in modernizing and maintaining its refineries and petrochemical plants to increase reliability and efficiency are significant. To deal with the need for constantly increasing demand, further efficiencies need to be unlocked — particularly in dealing with extending the service life of aging equipment amid supply chain delays, the lack of original equipment manufacturer (OEM) repair services, and long lead times for spare parts.
MAXIMIZING EFFICIENCY AND EXTENDING RELIABILITY OF EXISTING EQUIPMENT
In offshore and onshore operations, instead of only focusing on capacity, operators should prioritize enhancing productivity and maximizing profits through better management of current rotating equipment such as pumps, turbomachinery, and electric-driven drives such as generators. This involves addressing short mean time between failures (MTBF) to minimize downtime and achieve substantial cost and energy savings. There are several strategies that can be adopted to capture opportunities here with the support of an experienced OEM-agnostic independent service provider.
In a recent Sulzer case in Southeast Asia, a flare knockout pump on an offshore platform was experiencing reduced reliability due to abrasive sand causing excessive wear, reducing the MTBF to 12-18 months. This posed a significant risk of costly shutdowns if both pumps failed. A turnkey retrofit solution, with a tight deadline of 26 weeks, involved applying tungsten carbide coating to the impellers, upgrading bushings to ceramic, and refurbishing the motors. The retrofit not only matched the original pump footprint but also extended the MTBF, improved reliability, and reduced costs.
In another instance, a deteriorating 10-year-old 10.7-megawatt (MW) motor on a vessel, requiring urgent attention, was transported to a service center where it was refurbished with new stator coils, effectively extending its life by at least another decade. This work required precision and specialized expertise, demonstrating the importance of timely and expert intervention in extending equipment service life.
UNLOCKING OPPORTUNITIES VIA RE-RATES, RETROFITS, AND REVERSE ENGINEERING
The transition to renewable energy sources often leads to underestimating the value of optimizing existing oil and gas infrastructure as a means to reduce the carbon footprint. Investing in equipment retrofits, re-rates, and reverse engineering can yield benefits that last for years, in terms of ensuring equipment longevity, and extending their operational lifecycle despite the relatively short turnaround. Meanwhile, this sets the stage for more extensive overhauls during planned downtime.
In the Philippines, scattered island groups make equipment longevity and reliability even more crucial. Expert field services and specialized tools and equipment to deal with maintenance of ageing assets could make the difference in enhancing performance, minimizing downtime and excessive loss of capital. In cases where offshore platforms face issues with water injection pumps experiencing rapid wear, vibration, and downtime, effective fixes implemented with a hybrid cartridge to improve performance and energy efficiency through a hydraulic re-rate could lead to significant energy savings and CO2 reductions. In a Sulzer retrofit case study, this led to one pump saving 2 MW of power, cutting 5,536 tons of CO2 annually, while the other saved 1 MW, reducing CO2 emissions by 2,768 tons per year. In another example, a refinery needing repairs on a 22-year-old naphtha compressor that had been condemned by the OEM and stored without preservation saw a quick turnaround with reverse engineering. Rather than waiting 18 months for new parts, applying reverse-engineering to components, anti-fouling coating, and performing precise repairs, saw 50% of cost savings, compared to the cost of purchasing a new compressor. The refurbished compressor is now expected to last another 20-25 years, illustrating the value of reverse engineering in extending equipment life under tight deadlines.
OPPORTUNITIES IN MATURE OIL AND GAS ASSETS
To maximize oil recovery in mature sites, sustainable practices can also maximize output significantly. Enhanced Oil Recovery (EOR), where CO2 is injected into oil reservoirs to increase crude oil extraction from mature fields, can be applied where traditional methods are no longer economically viable. This involves high-pressure pumps and compressors to transport and inject CO2 into reservoirs that are designed to handle the corrosive nature of the process, particularly when combined with water and the high pressure required for injection.
For assets like the Malampaya Gas Field, injecting CO2 into mature gas reservoirs to maintain pressure and boost gas production can support enhanced gas recovery. Additionally, depleted gas fields are often utilized for CO2 sequestration, sometimes aiding in the recovery of residual hydrocarbons. Working with experts that can not only provide high-pressure compressors for CO2 injection and advanced gas processing technologies for CO2 removal, but can also offer gas processing technologies to ensure quality and marketability are vital.
Retrofitting pumps can also enhance the sustainability of EOR processes. Retrofits can be engineered to upgrade materials to resist water corrosion and erosion caused by sand content. Adjusting the capacity requirements for water injection as platforms age can also be achieved through specially engineered hydraulic re-rates.
EMBRACING EFFICIENCY FOR OIL AND GAS TO SUPPORT DEPENDABILITY
It’s important to recognize and act upon opportunities to improve the reliability and efficiency of existing rotating equipment within the oil and gas industry to increase dependability to meet demand. With sustainable methods of recovery from mature fields and retrofitting to support production changes due to market requirements such as new petrochemical products — it’s time to shift attention to these overlooked opportunities and leverage them to support the broader energy transition. In doing so, working with an OEM-agnostic independent service provider with deep application and industry expertise and timely project completion is essential.
Wong Chin Hean is the head of Services for Southeast Asia of Sulzer, a global leader in fluid engineering and chemical processing applications. The company specializes in energy-efficient pumping, agitation, mixing, separation, purification, crystallization and polymerization technologies for fluids of all types.